Традиционные методы испытаний, применяемые к металлическим трубопроводам, не подходят для тестирования вязко-упругих материалов, подобных полиэтилену. Трубы, изготовленные из таких эластичных материалов, демонстрируют «ползучесть» и релаксацию напряжений. Когда полиэтиленовый трубопровод находится под испытанием, некоторое падение давления неизбежно даже в системе без утечки. Рассмотрим рекомендации — методы испытаний под давлением, которые могут использоваться для оценки пластиковых трубопроводов на возможные утечки.
Тестирование полипропиленовых труб
Как рекомендовано нормативами, стандартное испытательное давление следует устанавливать в 1,5 раза выше номинального значения для компонентов, составляющих тестируемый участок. Если на участке включены механические фитинги, испытательное давление ограничивается значением — 20 бар.
Стандартное испытательное давление следует подводить к самому низкому уровню тестируемого трубопровода. Изначально трубопровод не должен подвергаться нагрузкам при заполнении, так как это может повлиять на результат испытания. Полиэтиленовые трубопроводы недопустимо подвергать испытанию, если температура стенки трубы меньше + 30°C.
Перед испытанием пластикового трубопровода необходимо убедиться, что насос имеет достаточную емкость для подъёма давления к испытательному уровню за время 10-20 минут. Этот момент обусловлен тем, что общее время испытания неразрывно связано со временем нарастания нагрузки.
Для обеспечения точного анализа данных испытаний под давлением следует использовать преобразователи с каротажным устройством и дисплеем.
Тестовые испытания – детальный расклад
Теоретически не существует технических оснований для ограничения длины испытываемого трубопровода. Так, на практике успешные испытания на перепад давления проводились с 5-километровой длиной трубы диаметром 1400 мм.
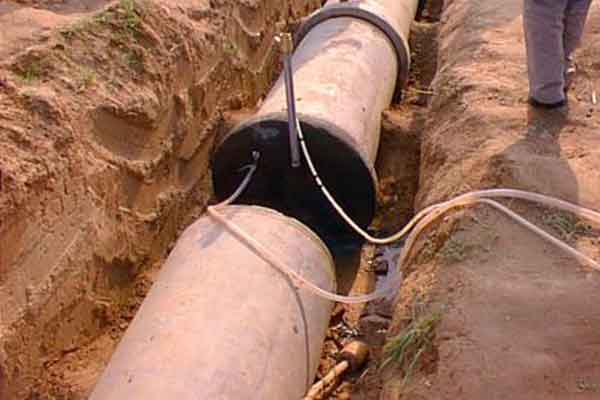
Длина испытательной секции обычно регулируется главным образом следующими критериями:
- увеличением электрической магистрали,
- продолжительностью испытания,
- количеством фитингов в системе,
- наличием воды для зарядки трубопровода.
Обычно рекомендуется предварительная испытательная фаза для стабилизации трубопровода и обеспечения насыщения, когда речь идет о водопоглощающих материалах трубопровода. Однако для пластиковых труб предварительный тест, как правило, не требуется.
Метод испытания давлением
При достижении испытательного давления, удовлетворительных условий минимального захвата воздуха и хорошей герметичности трубопровода за всё время теста, испытания считаются пройденными.
Опыт показывает, что повторное тестирование выполнять сложнее, потому что полипропиленовая труба уже растянута из-за эффекта «ползучести» от первоначально примененного давления.
Крайне важно обеспечить удаление воздуха перед тестированием. Чтобы обеспечить оценку захвата воздуха, оборудование, используемое для зарядки трубопровода, должно включать подходящий калиброванный расходомер с возможностью регистрации данных.
Минимальная продолжительность испытания по времени — один час или удвоенное значение времени нарастания давления.
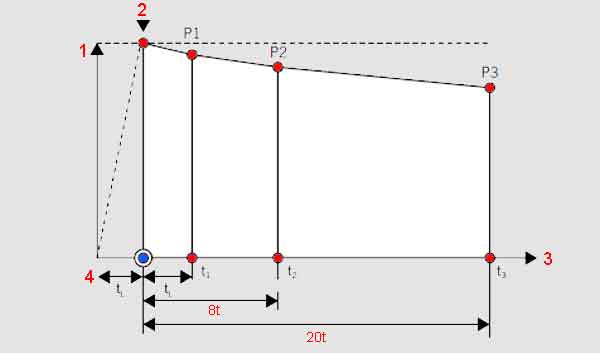
Время роста давления к испытательному значению (tL) используется в качестве эталона. Показания распада естественного давления регистрируются в заранее определенные моменты времени (кратные tL). Эти временные интервалы:
tL и 8 tL (t1-t2)
8tL и 20tL (t2-t3)
Проводят первое считывание P1 при t1,
Проводят второе считывание P2, при 8tL,
Проводят третье считывание P3 при =< 20 tL,
где: t1, t2, t3 — время нагрузки при значениях tL, 8tL, 20tL.
Начальное пусковое давление
Точки на трубопроводе, в которых отмечается значительный статический напор, могут повлиять на результаты испытания. Следовательно, значения давления, используемые в следующих расчетах, должны соответствовать значениям начального пускового давления (P0).
PA = Текущее (P) – Пусковое (P0)
PA1 = P1 — P0
PA2 = P2 — P0
PA3 = P3 — P0
Также требуется коррекция времени затухания для учета времени, затрачиваемого на повышение давления.
t1C = t1 + 0.4tL
t2C = t2 + 0.4tL
t3C = t3 + 0.4tL
где: t1, t2, t3 – скорректированное время.
Вычисляются отклонения (n) кривой затухания между двумя временными интервалами. Поскольку перепад давления имеет экспоненциальную форму, использование логарифмов необходимо при сравнении показаний, но использование карманного калькулятора – это всё, что требуется для расчетов «на месте».
n1 (t1 – t2) = log PA1 – log PA2 / log t2C – log t1C
n2 (t2 – t3) = log PA2 – log PA3 / log t3C – log t2C
Предполагается, что значения перепада (n) должны находиться между 0,07 и 0,09. Значения (n) могут иногда варьироваться от 0,06 до 0,10, что в определенной степени зависит от уплотнения засыпки траншей и содержания воздуха внутри трубопровода.
Значения (n) ниже 0,06 могут указывать на чрезмерную предварительную зарядку системы. В тех случаях, когда с течением небольшого времени наблюдается увеличение отклонения, этот момент указывает на утечки.
Если же за более длительный период времени отклонение превышает 0,13, здесь скорость перепада считается исключительно высокой.
Между тем не следует придавать большого значения показателям (n), указанным выше, которые приводятся в качестве руководства. Герметичность трубопровода может быть подтверждена только оценкой профиля перепада.
Для надёжного (герметичного) трубопровода перепад давления будет с постоянным логарифмическим отклонением, а любое постоянное увеличение отклонения во время испытания будет указывать на утечку.
Когда значения существенно меньше установленного минимума, этот фактор указывает на слишком большой объем воздуха внутри трубопровода. Понятно, что воздух необходимо удалять до момента, когда стартует проведение испытания пластиковых труб.
Завершение испытательной последовательности
По завершении испытательной последовательности, остаточное давление необходимо снижать медленно до значения, соответствующего предварительному заполнению трубопровода водой.
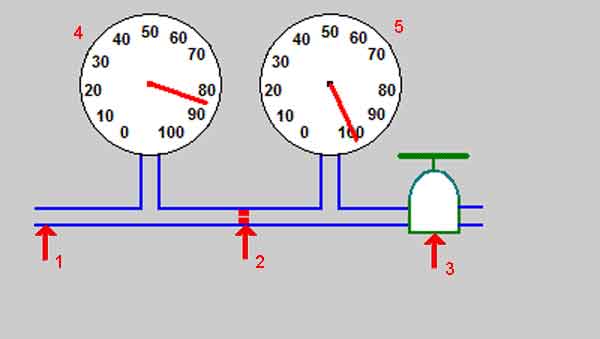
На случай повторного испытания пластиковых трубопроводов, тест не рекомендуется предпринимать до истечения времени, достаточного для того, чтобы трубопровод оправился от полученных нагрузок.
Это время восстановления пластиковой трубы, как правило, зависит от индивидуальных обстоятельств, но обычно руководствуются правилами использования периода времени, эквивалентного 5-кратному предыдущему испытательному периоду.
Введение пластиковых трубопроводов в эксплуатацию
Ввод в эксплуатацию новой либо отремонтированной сети питания и распределения обычно осуществляется в следующей последовательности:
- Очистка и/или свабирование водопровода.
- Заполнение и стерилизация.
- Промывка и/или нейтрализация.
- Заправка водопровода.
- Бактериологическая выборка.
- Приемочная сертификация.
- Введение и/или возвращение водопровода в эксплуатацию.
Последовательность для полиэтиленовых труб должна включать эти основные процедуры, но также может требовать конкретные условия (например, предварительное хлорирование водопроводной сети). Во всех случаях процедуры должны соответствовать требованию местного водного предприятия.
Сервисные трубы следует проверять с помощью муфт, соединенных с водопроводом. После испытания все эксплуатационные трубы должны быть подвергнуты окончательному процессу дезинфекции перед введением в систему водоснабжения.
Испытание газовых магистралей
Перед вводом в эксплуатацию все газовые сети подвергаются испытанию под давлением. Испытаниям подлежат любые части трубопровода, которые были обновлены или изменены. Важно чтобы один и тот же контрольный прибор (манометр) использовался для начального, промежуточного и конечного показаний.
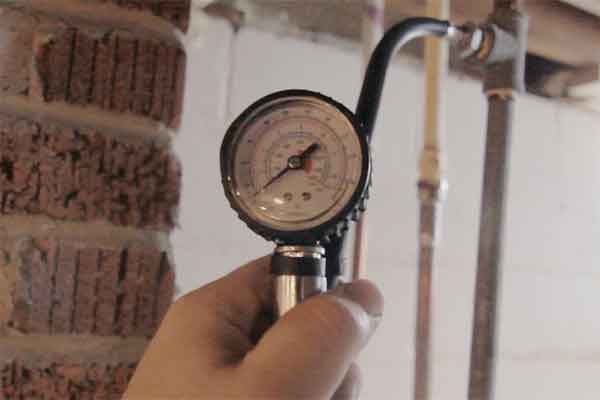
Любое испытание давлением полиэтиленового трубопровода допускает «ползучесть». Явление, при котором пластиковая труба расслабляется при сжатии, что приводит к небольшому увеличению объема и уменьшению внутреннего давления.
Существует два типа испытаний пластиковых труб:
- гидростатическое.
- пневматическое.
Для сетей, рассчитанных на работу с давлениями выше 2 бар, после гидростатического испытания следует пневматическое испытание. Для сетей с рабочим давлением менее 2 бар, допускается только пневматическое испытание.
Гидростатическое испытание давлением
Этот тест выполняется перед пневматическим (воздушным) испытанием. Механическая целостность основного или сервисного оборудования определяется путем полного заполнения водой трубопровода, подлежащего тестированию.
Затем введённую в магистраль жидкость доводят до испытательного давления. При обращении к этой методике необходимо избегать чрезмерных испытательных давлений, которые могут возникать из-за гидростатических напряжений в нижних точках.
Предварительное испытательное давление — 350 мбар, применяется до начала основного испытания, чтобы обеспечить общую целостность системы.
Если трубопровод заполняется гравитационным способом, следует подумать о необходимости отвода воздуха на верхних точках и удаления воды в нижних точках.
Кроме того, нельзя использовать чрезмерно аэрированную воду. По возможности, жидкость следует вводить в трубопровод через самую нижнюю точку.
Особенности заполнения трубопровода
До полного заполнения пластиковой трубы необходимо использовать непрерывный ровный поток воды. Заполнение не допускается, если температура воздуха составляет менее 2 — 3°C или есть риск получения такой температуры после заполнения.
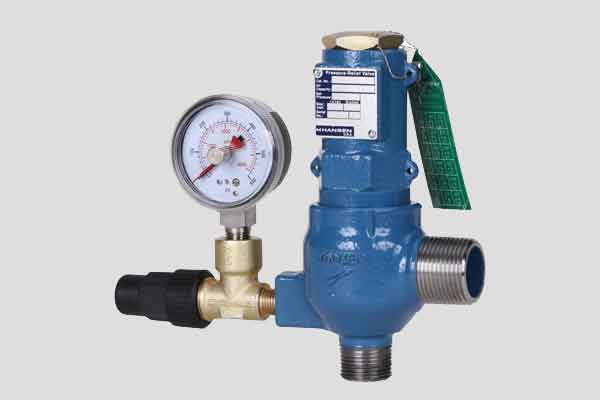
Как только вода закачана в трубу, температура должна быть стабилизирована до начала повышения давления к испытательному значению. Испытательное давление необходимо довести к самой высокой точке магистрали, где проверить с помощью манометра.
Периодический небольшой подъём давления необходим до начала испытательного периода, чтобы обеспечить линейность «ползучести» пластиковой трубы.
Затем стартует период тестирования. Давление и температуру грунта следует регистрировать через равные промежутки времени (например, каждые 15 минут) в течение испытательного периода.
Испытание успешно, если отсутствует потеря давления или существует постоянный, с небольшой скоростью спад, не превышающий 5% от испытательного давления за час теста.
Если результаты не соответствуют вышеуказанным критериям, рекомендуется продлить период тестирования, чтобы собрать больше данных.
После испытания вода удаляется из труб, как правило, с помощью специальных пневмо-подушек. Затем сухой воздух прогоняют через систему до тех пор, пока вся инженерная коммуникация не будет достаточно сухой.
Пневматическое испытание газовой магистрали
Это тест на утечку, который имитирует систему при максимальном рабочем давлении в газовых условиях. При проведении этого типа испытаний необходимо ориентироваться на барометрический контроль.
Для пластиковых труб диаметром более 63 мм, датчики-стойки должны быть соединены на концах новой магистрали и подключаться клапан сброса. Воздухом следует заполнять до тех пор, пока не будет достигнуто требуемое испытательное давление.
Перед началом испытательного периода температуру воздуха необходимо стабилизировать. Считывают показания манометров вначале испытательного периода и в конце.
Если период испытания длинный, может быть целесообразным взять несколько контрольных показаний в процессе теста. Таким образом, любые ранние признаки возможного провала испытания позволят избежать необходимости тестирования в течение полного периода.
С целью поиска утечек пластиковый трубопровод дозируют подходящим прослеживающим агентом (например, гексафторид серы или этилмеркаптан) под давлением до 350 мбар.
Затем по всей длине магистрали проводят проверку с помощью подходящего устройства обнаружения. После того, как утечка обнаружена, труба подлежит ремонту, после чего испытания давлением повторяются.
Для средне-нагружаемой трубы контрольное значение равно 75 мбар и не более 2 бар. Промежуточные значения могут составлять более 2 бар, но не более 7 бар. Контроль проводится от заглушенного конца магистрали в сторону впускного клапана сервисного регулятора.
Период тестирования должен соответствовать рекомендованному газовой службой. Снижение давления недопустимо.
Как только испытание завершено, воздух сбрасывают контролируемым образом до атмосферного состояния. Для труб диаметром не более 63 мм, работающих при относительно низких нагрузках (не более 75 мбар), воздух сбрасывается через регулирующий клапан-счетчик с одной стороны магистрали.