В пределах готовых участков траншеи бетонируют монолитные конструкции стен (рис. 1) или опускают сборные конструктивные элементы. После вскрытия очередного участка траншеи в него устанавливают арматурные каркасы, ширина которых должна быть на 10—12 см меньше ширины траншеи для обеспечения защитного слоя бетона достаточной толщины. Каркасы чаще всего делают сварными, включая иногда в их состав элементы жесткости. Для обеспечения точного положения каркасов в траншее к ним с боков приваривают салазки- катки, служащие направляющими при опускании. В верхней части каркасов закрепляют поперечные планки, которыми каркас опирается на грунт, а в нижней — короба для последующего сопряжения стен с междуярусными перекрытиями и днищем. В каркасах должны быть предусмотрены каналы для пропуска бетонолитных труб и закладные детали для грунтовых анкеров. Для обеспечения гладкой внутренней поверхности стен подземного сооружения на опускаемых в траншею арматурных каркасах иногда закрепляют листы из полимерных материалов. Перед опусканием каркасов размеры их должны быть тщательно проверены. Обычно каркасы устанавливают непосредственно перед бетонированием стен, поскольку глинистые частицы с течением времени осаждаются на арматуре, ухудшая ее сцепление с бетоном. Хотя глинистый раствор практически не окисляет арматуру, длительный разрыв во времени между установкой каркасов и бетонированием (более суток) неблагоприятно сказывается на качестве конструкции стен.
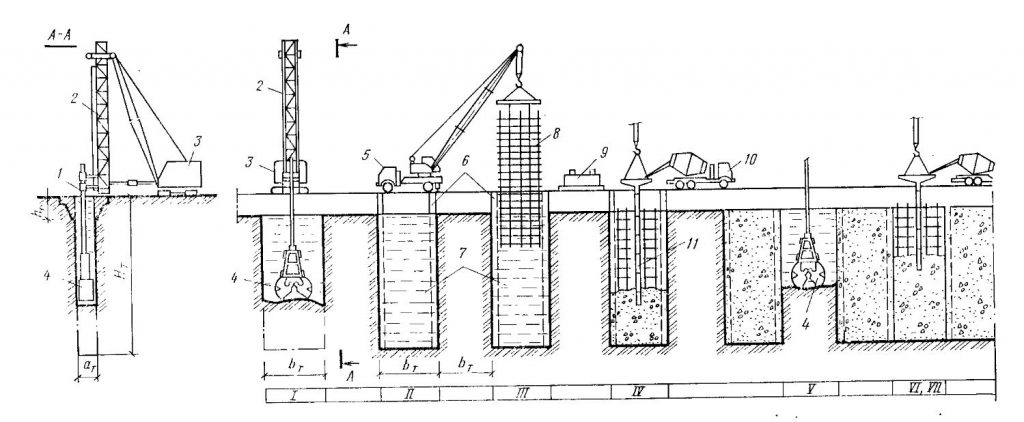
I — разработка грунта по глинистым раствором; II — опускание распределительных элементов; III — установка армокаркасов; IV — бетонирование стен и извлечение ограничителей; V — разработка грунтовых целиков; VI — установка армокаркасов; VII — бетонирование стен; 1- напорная штанга; 2 — копровая стойка; 3 — кран-экскаватор; 4- грейфер; 5 — кран; 6 — ограничители; 7 — глинистый раствор; 8 — армокаркас; 9 — отстойник; 10 — автобетоновоз; 11 — бетонолитные трубы.
После установки арматурных каркасов начинают бетонирование участков стен до низа перекрытия подземного сооружения. Технология укладки бетонной смеси такая же, как и при подводном бетонировании с применением вертикально перемещающейся трубы (ВПТ). Бетонная смесь марки не менее М200 должна быть достаточно подвижной и пластичной и иметь осадку стандартного конуса 16—20 см при крупности заполнителя до 50 мм. При этом водоцементное отношение должно быть не более 0,6, а срок схватывания — не менее 2 ч. Доставленную на строительную площадку бетонную смесь подают в траншеи через бункер по вертикальной бетонолитной трубе, опущенной между сетками арматурного каркаса. Обычно применяют стальные цельнотянутые трубы диаметром 219—300 мм со стенками толщиной 8 — 10 мм, состоящие из отдельных звеньев длиной 1 —1,5 м, соединенных плоскими быстроразъемными замками. Нижний конец бетонолитной трубы должен быть погружен в бетонную смесь не менее чем на 1 —1,5 м. Для предотвращения возможного заклинивания бетонной смеси в трубе на бункере закрепляют площадочный вибратор. Бункер с бетонной смесью устанавливают на вышке и закрепляют при этом на платформе, которая имеет возможность перемещаться в вертикальном направлении по стойкам вышки (рис. 2,а). Иногда участок траншеи бетонируют несколькими трубами одновременно (рис. 2, б).
Для подачи бетонной смеси в траншеи глубиной до 20 м наряду с вибробункером применяют телескопический укладчик производительностью 12—20 м3/ч (рис. 2, в). Он состоит из ковша- бункера, телескопической трубы, клапанного затвора и лебедки или крана для подъема ковша. Ковш устанавливают в вертикальное положение поворотом на 90°. При этом бетонная смесь начинает перемещаться по трубе. При бетонировании методом ВПТ по мере укладки бетонной смеси бункер или ковш вместе с бетонолитной трубой постепенно поднимают, следя за тем, чтобы конец трубы был заглублен в бетонную смесь. При этом трубу посекционно укорачивают. Бетонирование ведут практически непрерывно, допуская перерывы не более 2—3 ч.
Рассмотренная технология укладки бетонной смеси с применением вибробункеров и телескопических укладчиков имеет недостатки, связанные с цикличностью бетонирования, трудоемкостью монтажа и демонтажа звеньев бетонолитных труб, необходимостью использования только литых бетонных смесей с повышенным расходом цемента. В настоящее время созданы специализированные бетононасосы и бетоноукладчики непрерывного действия для бетонирования траншейных стен, снабженные телескопической стрелой, которая может подавать бетоновод в любую точку траншеи (рис. 2,г). При этом бетонная смесь укладывается снизу вверх под давлением методом напорного бетонирования, что позволяет получать бетон повышенной плотности, прочности и водонепроницаемости. В нашей стране применяют автобетоноукладчик поршневого типа БСГ1-25 производительностью 1—2 м3/’ч при глубине бетонирования до 20 м. Вытесненный бетонной смесью глинистый раствор по лоткам или трубам направляют в отстойник и после очистки подают на соседние участки траншеи. После бетонирования верхний слой бетона толщиной 30—40 см, загрязненный шламом и глинистым раствором, удаляют.
Отдельные участки траншейных стен, бетонируемые в разных захватках, должны быть сопряжены один с другим. Сопряжения могут быть жесткими или податливыми в зависимости от конструктивных особенностей подземного сооружения. Чаще всего их устраивают с применением специальных разделительных элементов— ограничителей, которые до бетонирования устанавливают по торцам участка траншеи и заглубляют в грунт. Помимо обеспечения совместной работы соседних участков стен ограничители должны предотвращать попадание бетонной смеси из одного участка траншеи в другой и гарантировать водонепроницаемость стыков.
Ограничители можно извлекать ‘после укладки бетона или оставлять в составе конструкции стен подземного сооружения. При глубине траншеи до 12 м применяют извлекаемые ограничители в виде стальных или железобетонных труб (рис. 3, а), а также балок прямоугольного (рис. 3, б) или эллиптического поперечного сечения. Чаще всего устраивают цилиндрические стыки, обеспечивающие плавное сопряжение соседних участков стен. Используют извлекаемые металлические ограничители замкнутого профиля из швеллеров с накладками из листовой стали, причем для образования полуцилиндрической шпонки к накладке приварена половина трубы (рис. 3,в).
Получил распространение вибрационной стык (рис. 3,г), который устраивают следующим образом. Инвентарную стальную трубу с приваренными к ней наружными продольными ребрами и фланцем в нижней части опускают в траншею. После бетонирования участков стен второй очереди трубу отрывают от бетона, оставляя так на некоторое время. После набора бетоном 50—60% проектной прочности в инвентарную разделительную трубу опускают бетонопровод, по которому подают жесткую бетонную смесь марок М200—М300 с осадкой конуса 5—6 см. По мере подачи бетонной смеси разделительную трубу извлекают вибропогружателем, а между соседними участками стен образуется плотный стык в виде буронабивной сваи.
В качестве неизвлекаемых ограничителей используют железобетонные балки прямоугольного поперечного сечения (рис. 3, д) или стальные двутавровые балки высотой, приблизительно равной ширине траншеи (рис. 3, е). Установленные вертикально с шагом 1,2—1,5 м, такие балки являются жесткой арматурой и избавляют от необходимости установки арматурных каркасов. Стыки между участками стен могут быть устроены с применением стальных диафрагм из полосовой стали, приваренных по торцам арматурных каркасов (рис. 3,ж).
На строительстве ряда подземных сооружений в Москве Глав- мосинжстроем использовались железобетонные ограничители-перемычки длиной 9, шириной 0,68, толщиной 0,3 м и массой 3,95 т (рис. 3,з). Применяют также ограничители с заделанными в них вертикальными полосами из полихлорвиниловой пленки толщиной 2—4 мм и шириной 20—25 см (рис. 3, и). Укрепленные металлическими стержнями диаметром 10—12 мм, такие полосы обеспечивают достаточно надежную связь отдельных участков забетонированных стен.
Делаются попытки создания жестких стыков между отдельными участками монолитных стен путем перекрытия соседних арматурных каркасов. Такие стыки могут работать на сжатие, растяжение, изгиб и срез и обеспечивают совместную работу смежных участков стены.
Устройство стен подземных сооружений из монолитного железобетона сопряжено с необходимостью выполнения довольно трудоемких операций. При этом не всегда удается добиться высокого качества конструкций стен и надежного сопряжения соседних участков. Кроме того, скорости возведения траншейных стен сравнительно невысоки. С целью повышения степени индустриализации строительства с применением технологии «стена в грунте» в последние годы начали применять сборные железобетонные панели, опуская их в заполненные глинистым раствором траншеи.
Применение технологии «сборная стена в грунте» способствует сокращению объемов земляных работ, уменьшению расхода железобетона, сроков и стоимости строительства. В зависимости от грузоподъемности кранового оборудования применяют тяжелые железобетонные панели толщиной 0,3—0,5 м, длиной до 10—15 ми массой до 20—30 т, стыкуемые только в продольном направлении, и легкие панели массой 5—6 т, объединяемые не только в продольном, но и в поперечном направлении по высоте стен. Возможно также устройство траншейных стен комбинированной конструкции, состоящих из монолитного железобетона в нижней и сборных панелей в верхней части траншеи.
Существуют различные технологические схемы возведения сборных стен в грунте, отличающиеся главным образом способом закрепления стеновых панелей в траншее. В нашей стране разработана технология закрепления панелей путем обетонирования зазора между ними и стенками траншей на высоту до 1 м с последующей забутовкой цементным раствором (снаружи) и песком (изнутри тоннеля) (рис. 4,а). За рубежом применяют технологию закрепления стеновых панелей медленно твердеющим дементно-бентонитовым раствором (прочность до 5 МПа), нагнетаемым в пазы между панелями, а также между стенками траншеи и панелями после установки последних, вытесняющим глинистый раствор и выполняющим связующие и стабилизующие функции. В составе медленно твердеющего раствора цемент, бентонит, песок и замедлители схватывания.
В ряде случаев траншею вскрывают участками длиной, превышающей ширину двух или трех панелей на 20—25 см (рис. 4, в). В заполненную глинистым раствором траншею нагнетают цементно-глинистый или цементно-песчаный раствор, объем которого определяют как разность объема разработанного участка траншеи и тех двух или трех панелей, которые должны быть установлены. Для подачи цементного раствора в траншею спускают металлическую трубу диаметром 10 см, длина которой на 0,5—1 м меньше глубины траншеи. Сверху закрепляют воронку, а внизу — горизонтальный патрубок с отверстиями. Выходящий через отверстия цементно-глинистый раствор, удельный вес которого превышает удельный вес глинистого раствора, вытесняет последний и занимает нижнюю часть траншеи. Далее устанавливают две или три панели, полностью вытесняя из траншеи глинистый раствор. Оставшийся цементный раствор заполняет швы между панелями и все остальные пустоты.
Панели опускают в траншею при помощи кондукторов и шаблонов в виде направляющих и опорных рам и соединяют по низу замковыми приспособлениями в виде стержней и клиновых крюков. До набора цементно-бентонитовым раствором определенной прочности панели удерживаются на направляющих стенках пионерной траншеи. Наружный зазор между стенками траншеи и панелями заполняют цементно-песчаным раствором, а внутренний зазор забучивают песком, щебнем или гравием (рис. 4, б). В этом случае вертикальные стыки между панелями заделывают насухо в процессе разработки грунта между траншейными стенками. Следует отметить, что применение сборных железобетонных панелей позволяет исключить трудоемкие работы по укладке и уплотнению бетонной смеси, повысить темпы строительства при высоком качестве подземных конструкций. Однако при этом возникают определенные трудности, касающиеся плотного примыкания панелей, тщательного заполнения всех пустот и т. п.
По окончании возведения траншейных стен производят геодезическую съемку расположения оси стены, определяют размеры последней и составляют исполнительную схему. Иногда контролируют качество монолитных стен в грунте ультразвуковым методом. При разработке грунтового ядра измеряют отклонения стен от вертикали и по высоте. Тангенс угла наклона вертикальной оси стены от проектного положения не должен быть более 0,01. Отклонения в толщинах не должны превышать для монолитных стен +50 или —20 мм, а для сборных стен ±20 мм. Максимально допустимые отклонения по высоте стен составляют ±50 мм.
После устройства траншейных стен до низа будущего перекрытия подземного сооружения вскрывают котлован с откосами или с временным креплением стен сваями или шпунтом. Дно котлована выравнивают по отметкам и покрывают слоем гравия, щебня или бетона. После этого во многих случаях по верху стен или буронабивных свай бетонируют продольные балки обвязки, на которые затем опирают перекрытие подземного сооружения.
Конструкцию перекрытия из монолитного железобетона часто бетонируют непосредственно на грунте, а сборные перекрытия монтируют колесными или гусеничными кранами. Готовое перекрытие покрывают гидроизоляцией и засыпают грунтом, восстанавливая дорожную одежду над подземным сооружением. После этого приступают к разработке грунтового ядра. Обычно грунт между траншейными стенами начинают разрабатывать не ранее чем через 2—3 сут после их бетонирования.
Технология земляных работ может быть различной в зависимости от вида и размеров подземного сооружения. При строительстве автотранспортных и пешеходных тоннелей разработку грунта производят в один прием со стороны портальных участков (рис. 5). При этом используют малогабаритные экскаваторы, бульдозеры, породопогрузочные машины и т. п.
При строительстве многоярусных подземных сооружений грунтовое ядро разрабатывают последовательно сверху вниз, выдавая разработанный грунт в бадьях краном через отверстия, оставленные в перекрытии.
Междуярусные перекрытия возводят после разработки грунтового ядра по схеме «снизу—вверх» или по мере разработки — по схеме «сверху—вниз».
В первом случае одновременно с разработкой грунта производят крепление траншейных стен расстрелами или грунтовыми ликерами, так же как при котлованном способе работ (рис. 6,а). После разработки грунта до проектной отметки снизу вверх возводят междуярусные перекрытия, демонтируя пояса и расстрелы. Основным недостатком такой технологии является необходимость дополнительного раскрепления траншейных стен.
Более прогрессивной является технология работ по схеме «сверху—вниз». При этом разработку грунта между стенами ведут на высоту каждого яруса подземного сооружения и сразу же возводят междуярусные перекрытия, которые выполняют также роль распорок, обеспечивающих устойчивость траншейных стен (рис. 6,б).
При строительстве многоярусных подземных сооружений по схеме «сверху—вниз» в ряде случаев применяют метод опускания перекрытий. При этом после устройства траншейных стен и сквозных колонн в уровне поверхности земли бетонируют или монтируют пакет из нескольких блоков перекрытий, временно подвешивая нижние блоки к верхним. По мере разработки грунтового ядра в пределах каждого яруса подземного сооружения промежуточные перекрытия последовательно опускают на проектные отметки (рис. 6, в). Опускание осуществляется при помощи домкратов, причем для пропуска сквозных колонн в блоках перекрытия предусмотрены проемы. После опускания пакета перекрытий на высоту очередного яруса верхний блок закрепляют на стенах и колоннах, а остальные блоки вновь опускают и закрепляют аналогичным образом.